Mechanical Design

Our Mechanical Design in OnShape
We utilized in-context design using OnShape to create a 3D model of our robot before construction
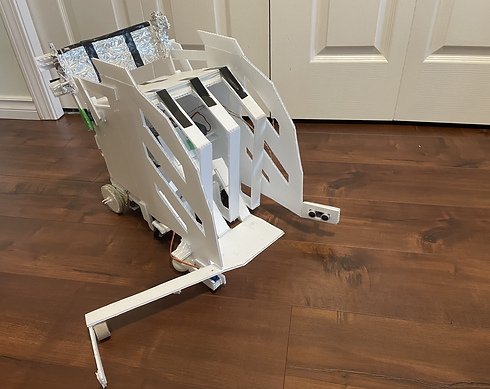
Our Final Design
We constructed our robot closely following the prototypes and models which we created
Design considerations
As per competition rules, the robot was to be constructed mainly from corrugated sheet plastic held together by hot glue. Thus, many different aspects were important to us in the consideration of the design. The following are attributes which we strove towards in our design:
-
The structure of the robot should be strong and rigid with the use of minimal materials so that it is not too heavy
-
The robots should be assembled from flat pieces that can be easily cut out from a sheet of corrugated platic
-
The internal components (where the electrical systems were housed) should be readily accessible after the robot was fully constructed
Structural Integrity
Trying to support a robot entirely from plastic and hot glue required us to utilize various techniques to strengthen our mechanical design. Several structures which we utilized to strengthen our robot included:
-
I-beams: for the support of servo motors
-
Cross hatching pattern on the wall and base to give the structure more strength
-
Triangle brackets at the connections between pieces to add rigidity and strength
-
Double layers of walls and base for additional structural rigidity




Manufacturability
Due to our limited supply of plastic, we took careful measures to ensure each of the components of our robot was manufactured precisely and accurately, without wasting any plastic.
To do so, we first compiled a list of all the cutouts which needed to be made. Then, we carefully planned these cutouts onto drawings in OnShape, ensuring that the pieces would use up the smallest amount of plastic as possible.
We also created a 3D model of our robot with the exact dimensions needed for each cutout to ensure that the components would mesh together without error during the assembly.
The final step was transcribing these cutout dimensions onto the plastic before cutting and assembling the pieces with hot glue.


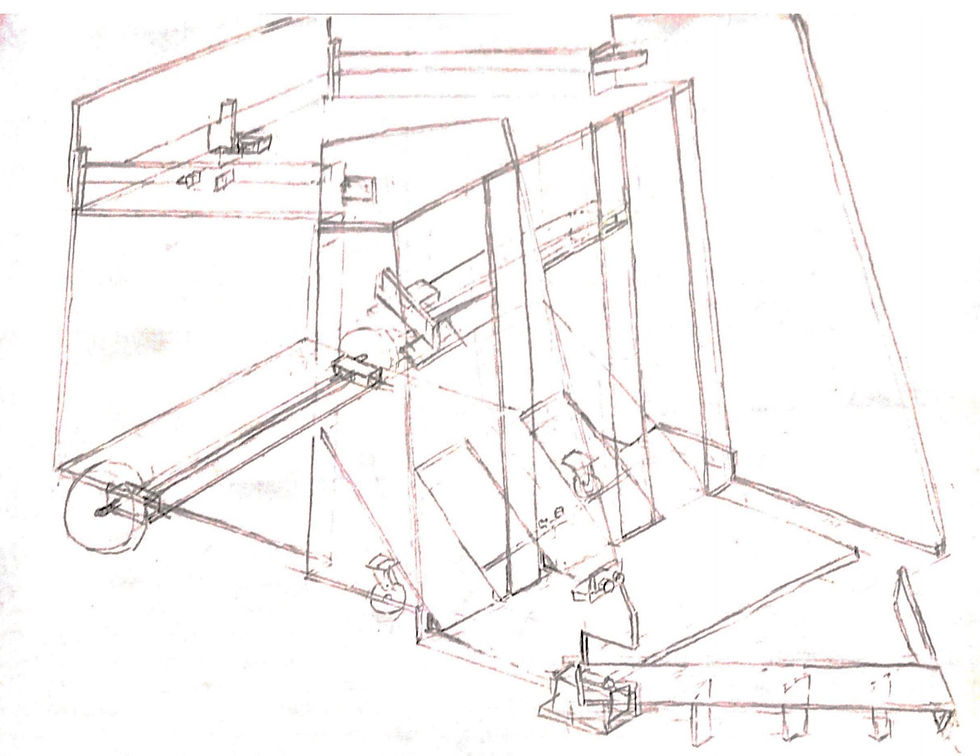

Accessibility
In order for the internal components to be readily accessible, we left the roof of the robot as a detachable component and left the back of the robot open. This way, the roof can be easily removed if the electrical components needed to be reached.
We also tried to centralize our battery packs (the heaviest component of our robot) so that the weight was equally distributed. We made sure each of our components was modular and organized so that they could be easily removed and put back together.
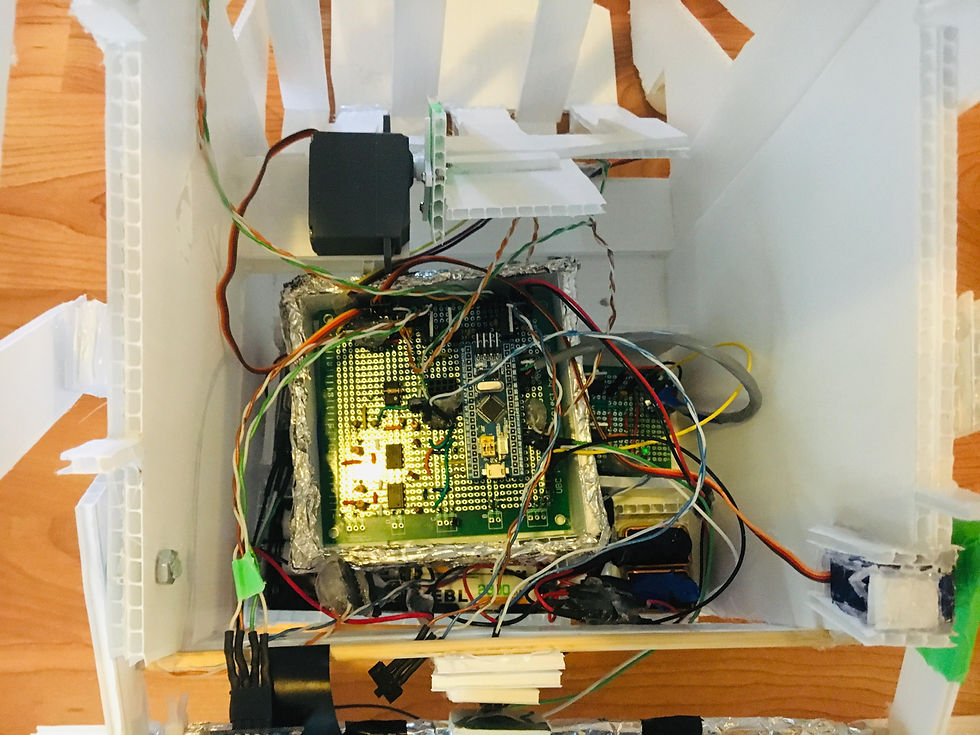
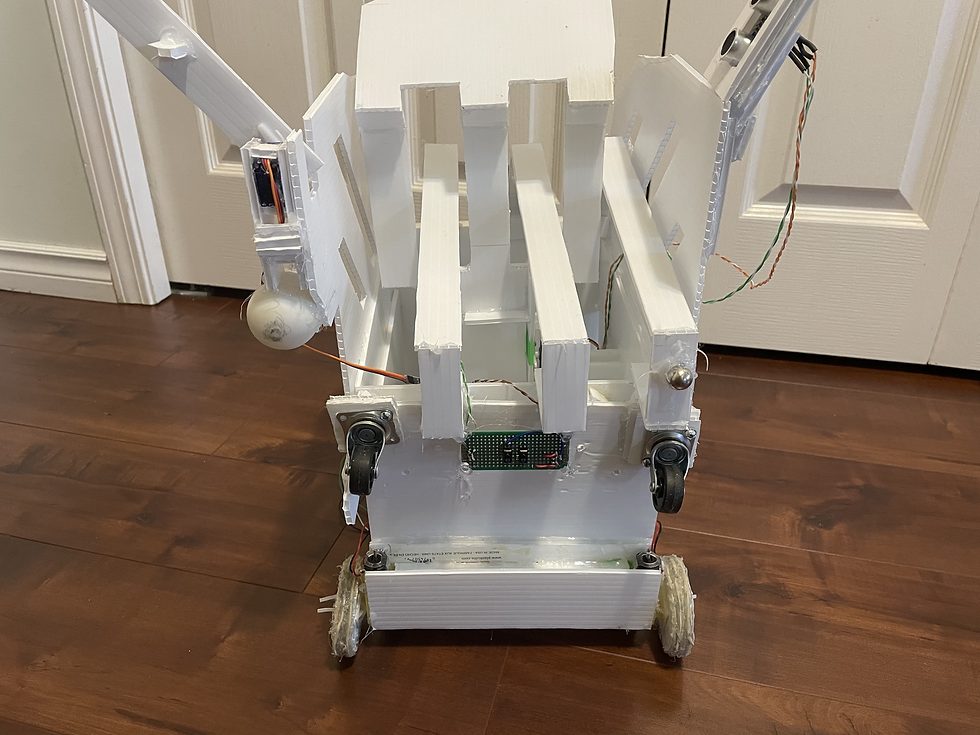

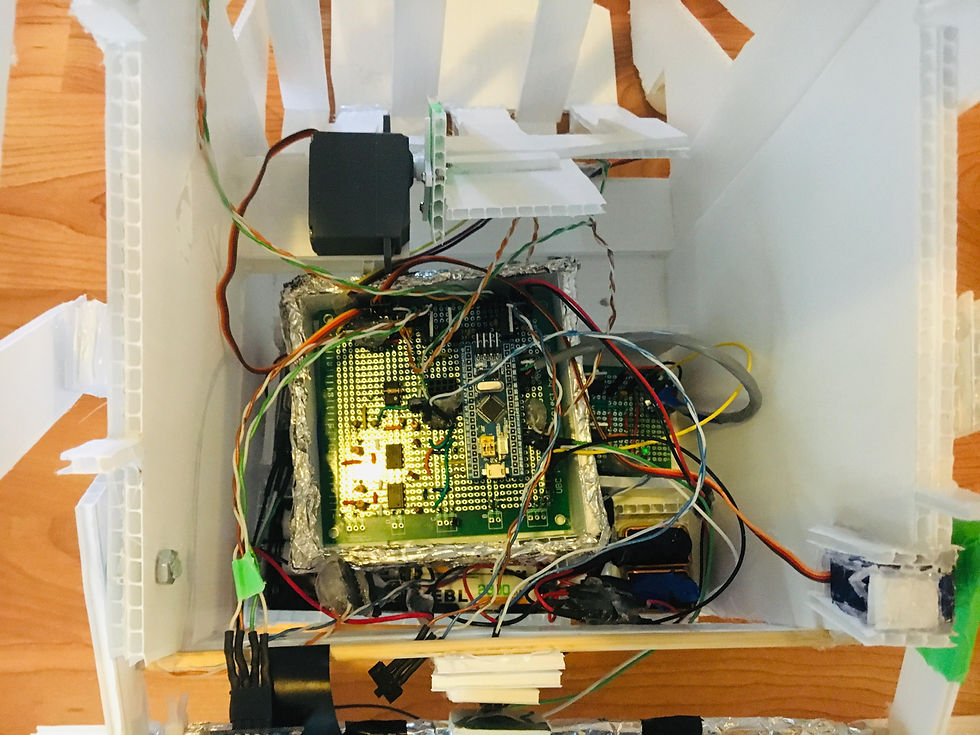